Quality isn’t just a standard
- it’s a commitment.
Every stage of our production process is carefully controlled to ensure precision, reliability, and consistency. We deliver products that meet the highest industry standards, because our customers deserve nothing less.
Your Success, Our Priority: Quality & Partnership at VIGO Photonics
At VIGO Photonics, you, our customer, are central to everything we do. As your needs evolve, we support upgrades or modifications to extend product value. Regular customer satisfaction surveys guide our improvement efforts, with every response leading to actionable changes. With us, you gain a partner who listens, delivers, and adapts—every step of the way.
Want to learn more? Connect with our team:
✔ Discuss a possibility of cooperation with our sales specialists: sales@vigophotonics.com – we're ready to answer your questions.
✔ Meet us at conferences – check our events to connect in person.
✔ Schedule a visit to VIGO Photonics – fill out our form to see how we work.
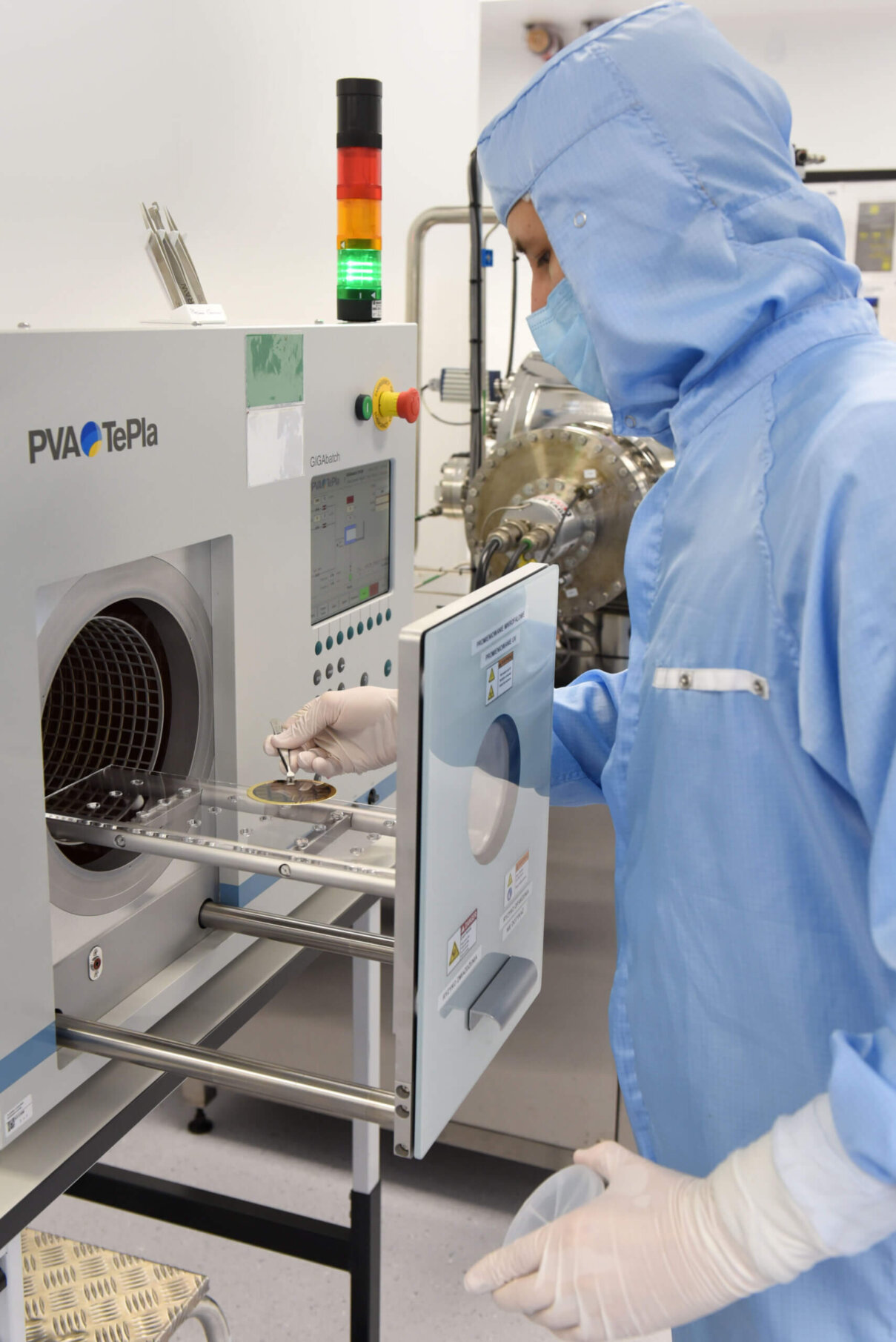
Quality System:
Our ISO 9001 certified Quality Management System (QMS) oversees every aspect, from designing and producing epi-wafers, infrared detectors, and modules, to R&D. Our certifications prove our adherence to the highest international norms. We operate with clear policies, including a strong anti-counterfeit measure, guided by VIGO Photonics values. We actively manage risks and opportunities, skillfully handle changes, and thoroughly check suppliers and components. Our commitment to quality, from concept to launch, includes meticulous quality control and a drive for continuous improvement.
Values and Rules:

Customer value → Create customer value

Quality → Keep standards high

Trust → Be honest and act with integrity

Leadership → Initiate and take responsibility

Team → Inspire and support

Effectiveness → Plan and accomplish

Knowledge → Dig to root cause

Continuous improvement → Improve and simplif

Ambition → Take on challenges

Perseverance → Learn on failures
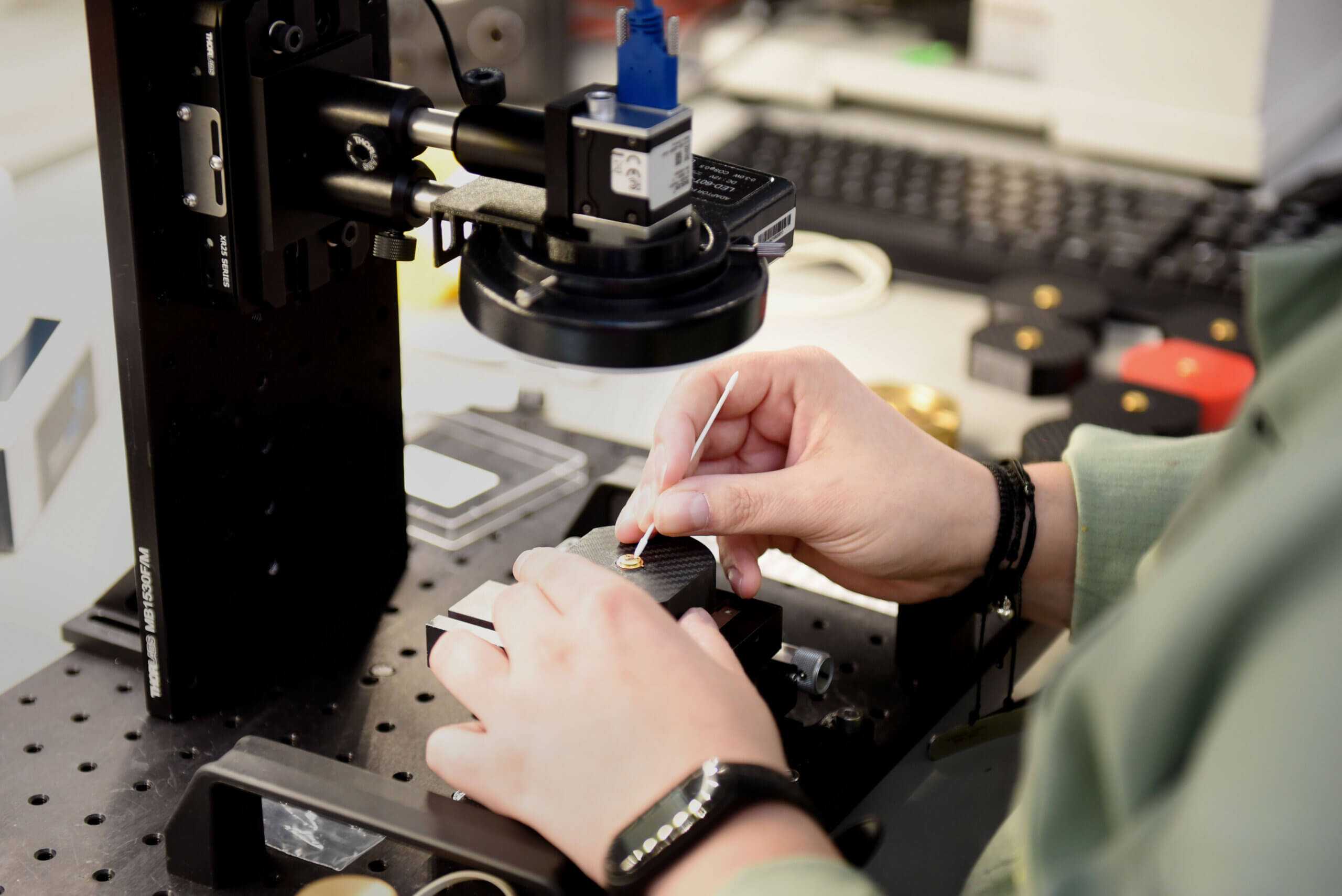
Risk and opportunity management:
At VIGO Photonics, we take a proactive and structured approach to managing risks and opportunities at every level of the organization — strategic, operational, project, and process. This ensures stability, compliance, and consistent alignment with our quality objectives.
We identify, assess, and monitor risks and opportunities across key areas such as strategy, regulatory compliance, QMS processes, R&D projects, FMEA analyses, and change management. Our actions support informed decisions, drive continuous improvement, and unlock growth potential, all while our robust Business Continuity Plan (BCP) ensures uninterrupted operations even in unforeseen circumstances.
Change Management:
At VIGO Photonics, we manage changes with full transparency and precision — always in line with customer requirements and industry standards. Whether it’s a product update or process improvement, we ensure smooth, effective implementation from start to finish.
What sets our approach apart?
✔ Full compliance with FFF (Form, Fit, Function) and customer-specific standards
✔ Clear communication of change scope, benefits, and responsibilities
✔ Structured change control system and approval process
✔ Risk analysis and mitigation actions built into every step
✔ Real-time tracking through Engineering Change Requests (ECRs)
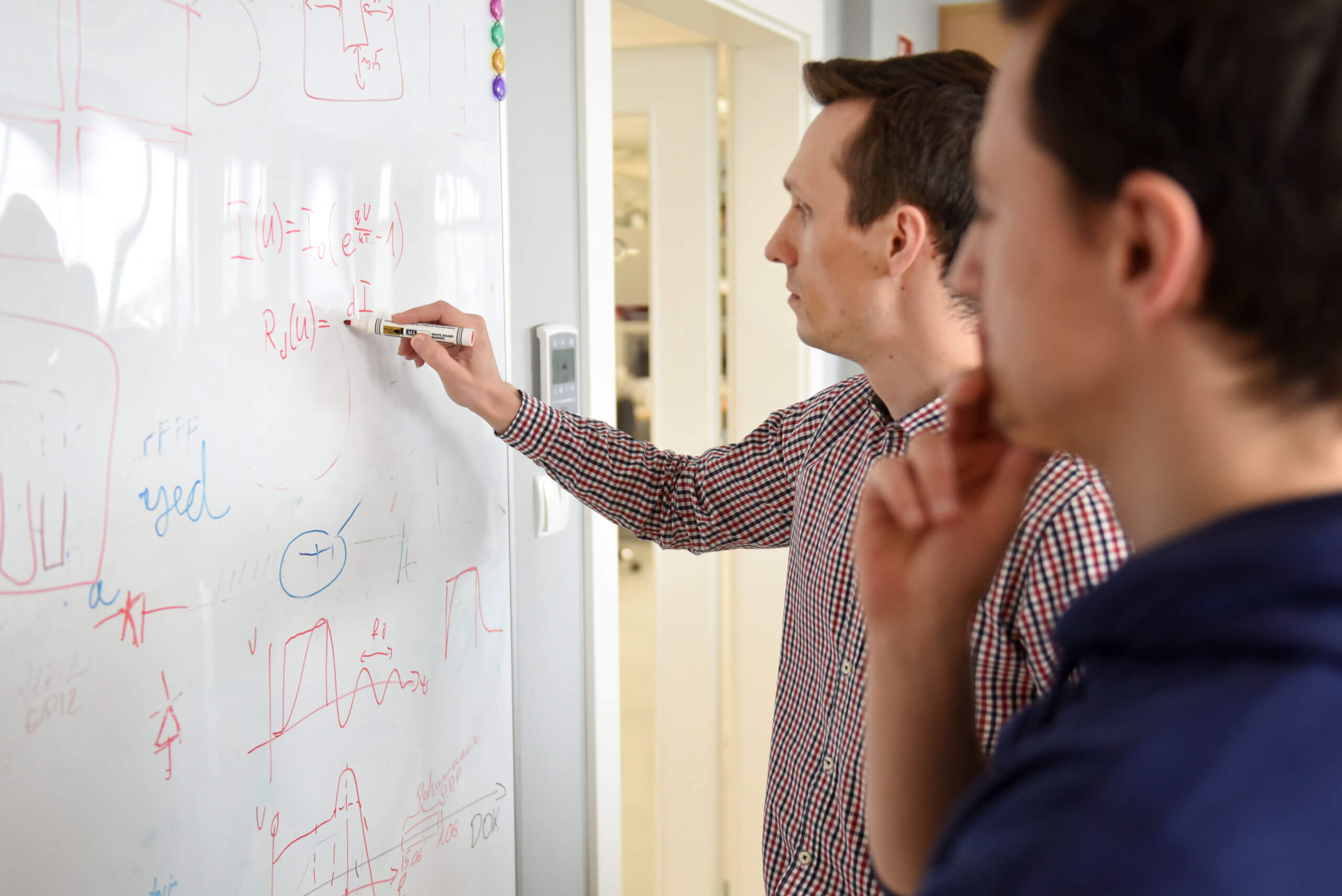
Our approach to working with suppliers and components:
Quality at VIGO begins with carefully chosen suppliers who meet the highest standards of reliability and performance. We qualify and monitor them through regular reviews and audits, addressing any issues with prompt corrective actions. Proposed changes are evaluated thoroughly to protect product integrity and ensure smooth implementation. This strong supplier management enables us to consistently exceed customer expectations and uphold our values of precision and excellence.
Every incoming component undergoes detailed inspection based on ISO-compliant sampling methods and tailored inspection plans. Our Quality Controller verifies key mechanical, optical, and thermal parameters using advanced tools such as spectrophotometers, optical systems, and ACR-meters. Full traceability is maintained, and nonconformities are resolved through root-cause analysis and improvement actions. Together, these processes ensure our products meet the highest standards from the very first step.
Quality from concept to launch:
Quality is embedded in every stage of our product development—from initial design to final validation. Using Advanced Product Quality Planning (APQP), we proactively align with customer and regulatory requirements, minimize risks, and optimize both performance and cost. This structured approach ensures we consistently deliver high-quality, reliable solutions.
Our designs are rigorously validated through prototype testing and refined to meet customer needs before full production begins. To ensure long-term durability, we conduct environmental and reliability tests under extreme conditions such as temperature, humidity, vibration, and thermal cycling. This thorough validation process guarantees our products are built to perform in real-world applications.
This diagram illustrates how these pivotal deliverables and their resulting customer benefits are generated and managed within this comprehensive, integrated framework
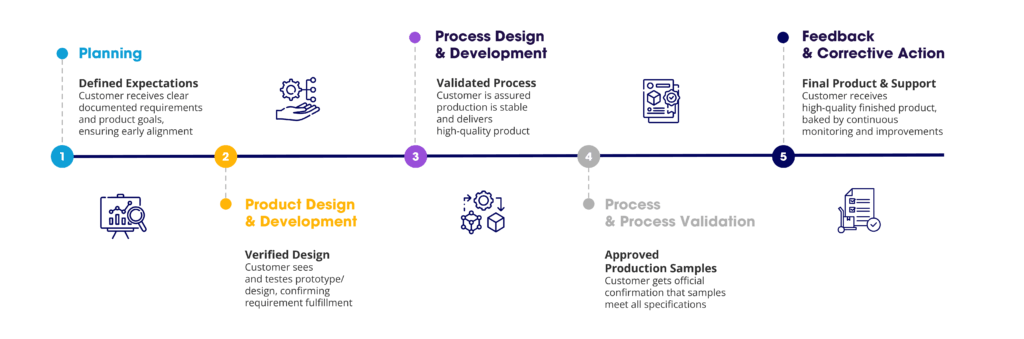
Our approach to quality control:
We build quality into every stage of development, from concept to final validation. Using Advanced Product Quality Planning (APQP), we ensure compliance with customer and regulatory requirements, reduce risk, and optimize performance and cost. Early prototype testing allows us to identify and resolve issues before production, ensuring the final product meets expectations.
To guarantee durability, we conduct rigorous environmental and reliability tests simulating extreme conditions like temperature shifts, humidity, vibration, and thermal cycling. This comprehensive approach ensures every product is ready for real-world challenges and reflects our commitment to dependable, high-performance solutions.